Speciality Chemicals For Metal Pre-Treatment
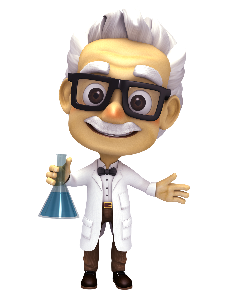
‘Bringing New Ideas To The Surface’
The highest quality finish to your manufactured metal products, whether they are of mild steel, galvanised steel, aluminium, or an aluminium alloy, begins with the best quality pre-treatment chemicals and production processes.
PreTreat has a wide range of solutions – honed over many years and frequently reviewed & updated – for every stage of your metal manufacturing journey.
Pre-Treatment Solutions for Industrial Applications
The present range of more than 100 standard products covers all types of phosphating and alternative environmentally friendly ‘nano-technology’ solutions, as well as specialist cleaners and related processes.
The comprehensive range of PreTreat pre-treatment products now include:
- Amorphous iron phosphates, zirconium, and titanium pre-treatments. Heavier manganese and zinc phosphate conversion coating processes for iron and steel
- Dry-in-place (non-rinse) conversion processes for most metals
- Chromate and chrome-free conversion processes for zinc surfaces, aluminium, and its alloys
- Pre-cleaners and degreasers for ferrous materials zinc and zinc-coated steel
- Pre-cleaners, cleaner/etchants and de-smut processes for aluminium
- Final rinse additives to enhance the corrosion protection afforded by conversion coatings
- Combined ‘laser oxide’ removal and phosphating processes for paint bonding after laser cutting and prior to coating
- Various etch primers, de-watering fluids and effluent treatment chemicals, etc.
Available as immersion or spray processes, PreTreat conversion coatings improve the adhesion of paint and plastics finishes and provide a barrier against corrosion should the finish become scratched, chipped or otherwise damaged.
The fine crystalline nature of the coating also reduces friction between moving metal interfaces and has a natural ability to retain mineral and vegetable lubricants, imparting wear resistance to moving metal interfaces and facilitating the cold deformation of metals.
Speciality Chemicals For Phosphating
The selection of pre-treatment depends on the conditions of service required by the end product. If the application is for internal use or low to moderate exposure requirements, iron phosphates can normally be used.
If the application is for external use or a hostile environment, chromates, or alternative environmentally friendly ‘nano-technology’ processes, should be considered.
Light-Weight Iron Phosphates
These processes can be applied to steel, zinc, and aluminium in mixed metal production.
The coatings produced from iron phosphate solution are amorphous in nature giving an iridescent appearance ranging from yellow through to blue. The conversion coating produced is very light, giving coating weights in the range of 0.2 to 0.8 gms per square metre, depending on the type of process used.
The iron phosphate processes are very economical in use, easy to control, operate at low temperatures, and do not present a major effluent problem.
Zinc Phosphates
These processes are mainly to treat steel but will also treat zinc and aluminium in mixed metal production.
The coatings produced on steel are crystalline, grey in colour and extremely adherent. The conversion coating produced is light to medium, giving coating weight usually in the range 1.5 to 6.0 gms per square metre.
Some zinc phosphate processes are susceptible to harsh cleaning methods which can be overcome by using a conditioning agent in the rinse prior to phosphating. An alternative would be to use a calcium-modified zinc phosphate which produces fine uniform coatings even after harsh cleaning.
In comparison with lightweight iron phosphates, zinc phosphates are slightly more expensive to operate, requiring closer control, form more sludge as a by-product, and may give rise to effluent problems.
The iron phosphate processes are very economical in use, easy to control, operate at low temperatures and do not present a major effluent problem.
Zirconium Pre-Treatment Technology
This process can be used in mixed metal production and treat steel, zinc and aluminium. The process produces lightweight coatings with very little sludge and can be used at low temperatures.
A typical example would be FASBOND 1315– High-Performance Lightweight Iron Phosphate.
FASBOND 1315 is a liquid, high-performance, lightweight Iron Phosphate conversion process designed to simultaneously degrease and phosphate in one operation. The process will treat iron, steel, zinc and aluminium in mixed metal production.
Pre-Treatment Cleaners & Degreasers
We formulate and manufacture acid, alkaline and neutral Cleaners and Degreasers for etching and desmutting.
- Acidic: for de-rusting and etching of aluminium. The de-rusting of mild and galvanised steel components. (An example of this is our PC100, a combined degreaser and etch for aluminium that will remove all oils and soils from the extrusion process and leave the surface ready for the conversion coating stage. All at ambient temperature).
- Alkaline: For demanding degreasing operations, low temperature, and low concentration, thus saving energy
- Neutral single-stage cleaners, for parts cleaning or inter-operational stage cleaning
- Safe solvent cleaners
- Non-Etch cleaning for aluminium and its alloys.
They come in the form of liquid and powder for spraying and immersion and they are for low-temperature and low-concentration operation.
Cleaners and degreasers are very effective; when applied to grease stains, they chemically react with the grease particles and produce a deep clean.