Salt Spray Testing Service
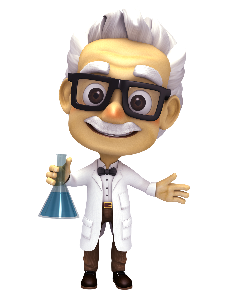
‘Bringing New Ideas To The Surface’
PreTreat’s Salt Spray Testing service is one of its most popular as it can provide a valuable assessment to the majority of manufacturers producing metal parts requiring a finished coating.
The salt spray test is an accelerated corrosion test that produces a corrosive attack on the coated samples in order to predict its suitability for use as a protective finish.
It’s a low-cost service, only charging per hour of testing duration.
We offer a complimentary Salt Spray Testing service to PreTreat customers.
Ensuring Corrosion Resistance
Coatings provide corrosion resistance to metallic parts made of steel, mazak or brass. Since coatings can provide a high corrosion resistance through the intended life of the part in use, it is necessary to check corrosion resistance by other means.
The salt spray test is an accelerated corrosion test that produces a corrosive attack on the coated samples in order to predict its suitability for use as a protective finish. The appearance of corrosion products (oxides) is evaluated after a period of time.
Test duration depends on the corrosion resistance of the coating; the more corrosion-resistant the coating is, the longer the period of testing without showing signs of corrosion.
Our Salt Spray Testing provides rapid results to help you check and improve your coatings’ corrosion resistance.
Our Simple Pricing Structure
We are unique amongst corrosion testing service providers in the UK in that:
- We only charge a fixed price per hour of £0.35p
- There are no set-up costs
- There is no minimum test duration
- We charge per component.
What this means in real terms is that should there be a premature failure in a testing programme – hopefully not – you will only pay for the testing time up until that point. This is opposed to the industry standard where you are charged for a set minimum of hours, usually 1000, whatever the outcome.
FOR EXAMPLE – 3 x panels for 1000 hours = £1050.00
However, should the panels unfortunately fail at 250 hours, we would only charge for that duration: £262.50.
Substrates & Coatings That Can Be Evaluated
- Painted substrates (powder coated / wet paint systems)
- Pre-treated substrates under a powder coating / paint system (tested for longevity)
- Complex high-build paint systems (for superior corrosion resistance)
- Zinc and zinc-alloy plating (see also electroplating). See ISO 4042 for guidance
- Electroplated chromium, nickel, copper, tin
- Coatings not applied electrolytically, such as zinc flake coatings according to ISO 10683
- Organic coatings.
And those that can’t…
- Hot-dip galvanized surfaces are not generally tested in a salt spray test (see ISO 1461 or ISO 10684). Hot-dip galvanizing produces zinc carbonates when exposed to a natural environment, protecting the coating metal & reducing the corrosion rate
- The zinc carbonates are not produced when a hot-dip galvanized specimen is exposed to a salt spray fog, therefore this testing method does not give an accurate measurement of corrosion protection. ISO 9223 gives the guidelines for proper measurement of corrosion resistance for hot-dip galvanized specimens.