Pre-Treatment Chemicals For Mild & Galvanised Steel
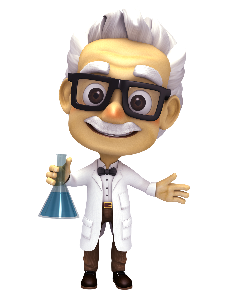
‘Bringing New Ideas To The Surface’
Is your company currently using traditional Iron Phosphates or Zinc Phosphates for the pre-treatment of mild and galvanised steel.
If so, PreTreat can offer alternatives that are Phosphate-Free and at the same time reduce your costs, processing time, and hazardous waste, whilst maintaining or even improving the quality of your finished product.
Pre-Treatment Solutions for Mild & Galvanised Steel Applications
The selection of phosphate depends on the conditions of service required by the product and, in some cases, conventional iron phosphate processes certainly still have their place.
However, there are now phosphate-free alternatives, including PreTreat Ltd’s proprietary brands FASBOND® 1701 and WALTERISATION® 7460, that can save time and money, and are kinder to the environment.
Replacing an iron or zinc phosphate process with FASBOND® 1701 we have achieved: lower chemical usage by 10%, significantly less or no flash rusting between stages, much lower iron build-up in the bath, fewer dumps, no paint problems due to “pin holes” caused by the residues, and significantly easier to control and titrate: <3 min vs > 20 min.
CONVENTIONAL IRON PHOSPHATE | PHOSPHATE FREE PROCESS |
---|---|
Cleaner/Coater | FASBOND® 1701 |
Rinse | Rinse |
Seal | WALTERISATION® 7460 |
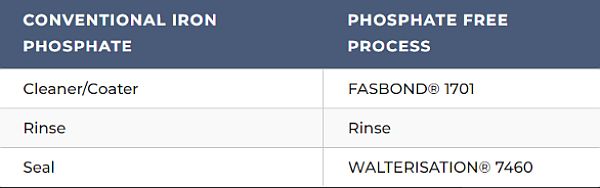
Available as immersion or spray processes, PreTreat conversion coatings improve the adhesion of paint and plastics finishes and provide a barrier against corrosion should the finish become scratched, chipped or otherwise damaged.
FASBOND® 1701
… is a titanium / zirconium based combined degrease process, which operates similarly to a conventional iron phosphate pre-treatment process.
In independent corrosion testing results of up to 1000 hours neutral salt spray on iron and steel, and 3000 hours on aluminium, when used with a ‘dry-in-place’ rinse sealer WALTERISATION® 7460
FASBOND® 1701 is a very efficient pre-treatment process.
It has the following features and benefits:
- Single-pack liquid – giving ease of handling and control –that saves time and the possibility of mistakes being made
- High corrosion resistance – on ‘Q panels’ testing to ASTM B 117 results of 1000* hours on mild steel and 3000 hours on aluminium have been achieved
- Multi-metal – can treat a variety of substrates, in any combination thus is futurized and able to cope with to-days and long-term production requirements, as only one process only is required
- Low temperature – operating range 15 – 35oC giving energy savings with resulting lower fuel bills
- Short process time – increased throughput – lower unit costs and higher production
- High chemical concentration – lower chemical usage – very cost-effective in use
- Very long bath life – bath life from experience is between 50 – 100% longer than conventional processes
- Very low sludging – sludge generation is between 50 – 75% less than conventional processes
- Spray or Immersion Application.
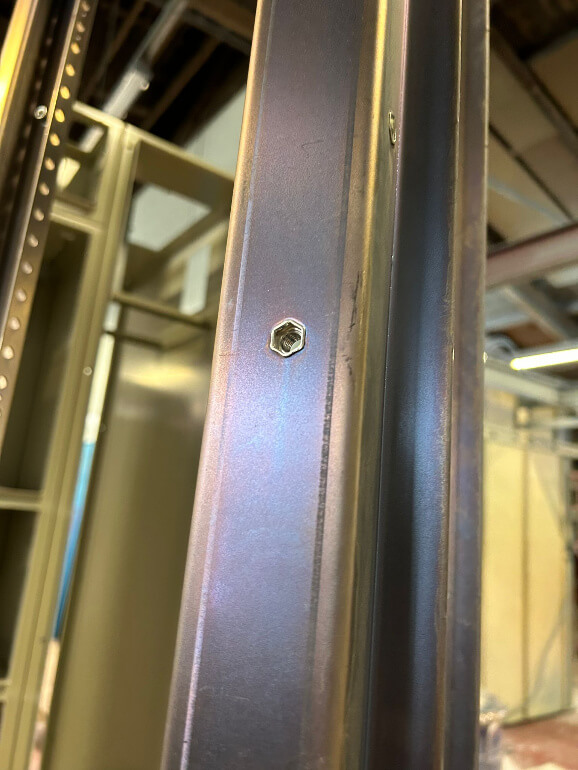
IRON PHOSPHATE | FASBOND 1701 | |
---|---|---|
Phosphate-Free | No | Yes |
Sludge-Free | No | Yes |
Ambient Operation | Not Usually | Yes |
Non-Hazardous | No | Yes |
Can be Declassified | No | Yes |
Needs Cleaning Step | Not Usually | Yes |
Needs Rinsing Stage | Yes | No |
Overall Cost | Higher | Lower |
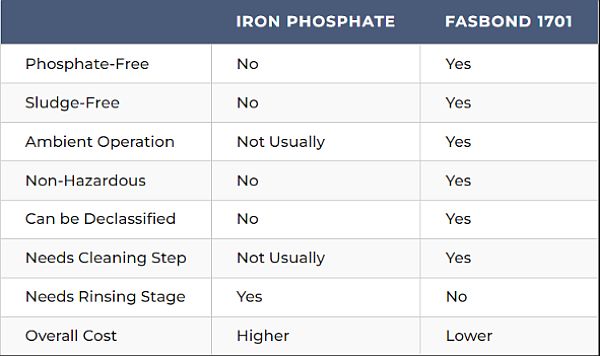
FASBOND® 1701 is a single-pack cleaner/coater – it degreases and phosphates in one action; specifically formulated for the simultaneous degreasing and phosphating of steel, aluminium and zinc-coated steel substrates by spray application in a 3 or 4-stage spray pre-treatment plant, or by immersion.
Degreasing capability may be further enhanced by the addition of Additive 354.
The process is free from heavy metals and molybdate.