Chemical Dosing & Control Equipment
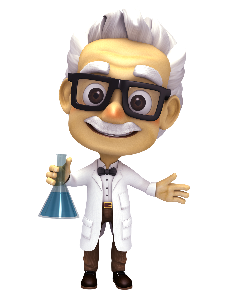
‘Bringing New Ideas To The Surface’
Manufacturing businesses are now, more than ever before, looking to control their production processes more precisely to reduce costs while at the same time maintaining, or even improving, the quality of their finished products for their customers.
PreTreat are able to supply, fit and set up chemical controllers for process tanks and rinses and offer continued support through any issues that may sometimes arise.
Chemical Dosing Equipment
Automatic Ion Control is an accurate and reliable method for automatic control of metal treatment baths, using the latest technology.
Installation is quick and simple, and minimal subsequent operator involvement leads to a cost-effective means of running a metal treatment process which is relatively free of human error.
The benefits of installation include:
- Peace of mind the chemical solution is at the correct operating strength
- Immersion and spray applications can be controlled accurately
- No handling of chemicals by operators
- Each unit is a bespoke manufacture, suitable to customer’s individual needs.
Full Commissioning and Warranty Included
Automatic Ion Control uses an ionic sensor to assess the % concentration or activity in a process bath. In general, normal operation is in % Concentration Mode, which relies on the correlation between changes in ionic mobility in solution and any change in concentration of the process bath.
The use of the ionic sensor in alkaline etch baths presents a relatively complex situation, due to the various chemical equilibria involved. For this type of bath, the meter operates in Activity Mode, which allows compensation for the different activity coefficients of the ions in solution.
After initial calibration for the specific concentration and temperature of the bath, the operation is virtually maintenance-free.
Control Equipment
It’s common sense that accurately controlling the dosage of chemicals to your metal pre-treatment process plant will ensure the most cost-effective and efficient production of high-quality finished goods.
However, the control of rinse waters is also an important factor to all of the above and many manufacturers now have an effective controller for the rinse stage operation too.
This installation can reduce water consumption by up to 33% and ensures the quality of the water is adequate for chemical processing.
Operator error is eliminated, as the units are controlled by the same power source as the main plant.
Quality improves as well; many cases of osmotic blistering formation have been overcome by controlling poor rinse water.